In the realm of hygienic production, staying competitive requires embracing cutting-edge trends. Advanced sanitization technologies like UV sterilization and automated cleaning systems are essential for maintaining high cleanliness standards. Robotics and automation reduce contamination risks by minimizing human contact. Implementing comprehensive traceability systems ensures product transparency and regulatory compliance. Smart packaging that extends shelf life and intelligent labeling that indicates freshness are becoming crucial. Additionally, adopting hygienic design principles for equipment and facilities, coupled with ongoing employee training in cleanliness, is vital. Companies that integrate these practices not only meet stringent safety standards but also lead in market competitiveness. As consumer awareness and regulatory requirements around hygiene and safety increase, industries involved in production—particularly in food, pharmaceuticals, and cosmetics—must adapt to maintain their competitive edge. Here are some crucial trends in hygienic production that businesses should consider to stay ahead: The adoption of advanced sanitization technologies such as UV sterilization, ozone treatment, and automated cleaning systems is on the rise. These technologies ensure high levels of cleanliness and reduce the risk of contamination without relying heavily on manual labor. Incorporating automation and robotics into production lines can significantly minimize human contact with products, thereby reducing the risk of contamination. Robots can perform tasks such as sorting, packaging, and even quality control inspections under sterile conditions, enhancing overall product safety. Consumers and regulators increasingly demand transparency in the production process. Implementing comprehensive traceability systems allows companies to track every aspect of the production process, from raw materials to final products. This not only boosts consumer confidence but also simplifies recall processes if necessary. Innovative packaging solutions that extend shelf life and maintain product integrity without compromising on safety are key. Technologies such as active packaging, which can control the atmosphere inside packages, and intelligent packaging that indicates product freshness or exposure to contaminants, are becoming increasingly popular. Staying updated with the latest regulations and standards is crucial. Software solutions that can help manage and ensure compliance are invaluable. These systems can alert businesses to changes in regulations and help manage documentation and certification processes efficiently. Adopting hygienic design principles for machinery and plant layout can significantly reduce contamination risks. Equipment designed for easy cleaning, with minimal ridges, joints, and materials that resist bacteria build-up, can streamline sanitization processes and reduce downtime, use certified hygienic components. Continuous training programs for employees on the latest hygiene practices and safety protocols are essential. Cultivating a culture of cleanliness and safety among staff ensures that best practices are followed consistently and diligently across all levels of operation. As sustainability becomes a global priority, integrating eco-friendly hygienic practices is vital. This can include using environmentally friendly cleaning agents, reducing water usage with efficient cleaning systems, and implementing waste reduction strategies. By embracing these trends, companies in hygienic production can not only meet the increasing standards of product safety and quality but also differentiate themselves in a competitive market. Critical maintenance of the highest standards of cleanliness involves clear protocols, thorough training, and the use of high-quality products and equipment. Routine and deep cleaning schedules, effective waste management, and strict personal hygiene are essential. Regular inspections, feedback mechanisms, and detailed documentation ensure ongoing adherence to cleanliness standards. Compliance with health regulations and continuous improvement through new technologies and practices are vital. In environments like hospitals, maintaining cleanliness prevents infections and promotes safety. This commitment ensures a safe, healthy, and productive environment for all.
Embracing Innovation: Key Trends in Hygienic Production to Maintain Market Competitiveness
Trends to Maintain Your Competitive Edge in Hygienic Production
Advanced Sanitization Technologies
Automation and Robotics
Traceability and Transparency
Smart Packaging Solutions
Regulatory Compliance Software
Hygienic Design Principles
Employee Training and Culture of Cleanliness
Sustainable Hygienic Practices
Increasing standards
Critical maintenance of the highest standards of cleanliness
Contact
Articles
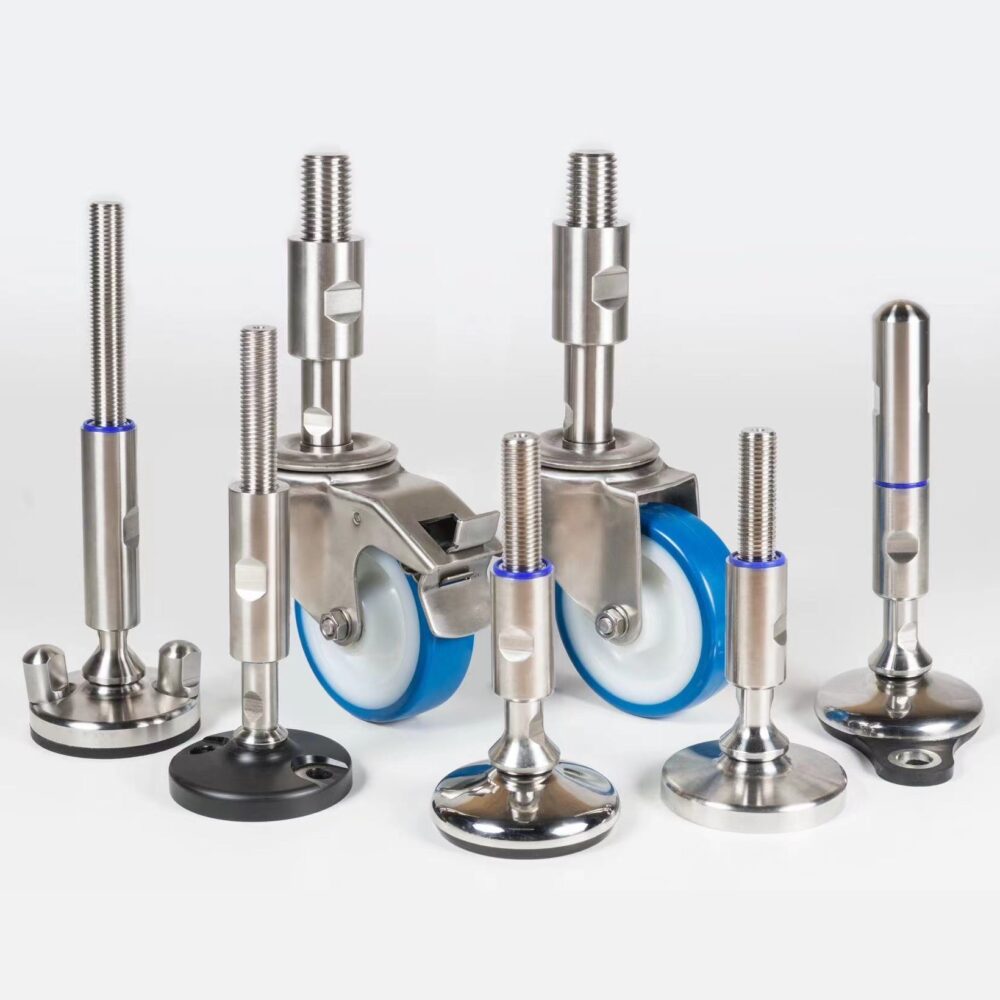