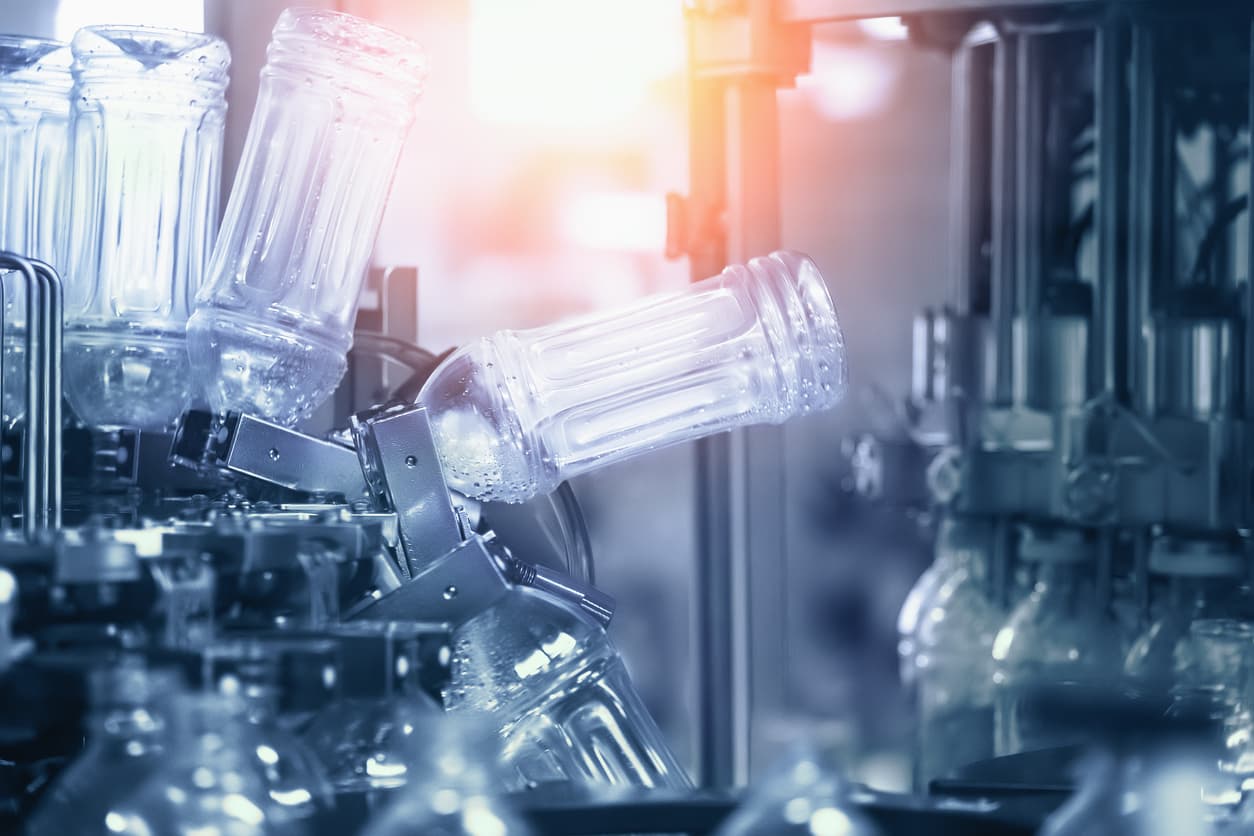
Sanitary Machinery Parts in the Food Processing and Pharmaceutical Industry
In the food processing and pharmaceutical industry, maintaining strict hygiene standards is vital to ensure consumer safety and product integrity. One crucial aspect of hygiene is the use of sanitary machinery parts. These components are specifically designed to meet stringent cleanliness requirements, prevent contamination, and safeguard the quality of food and pharmaceutical products. This article highlights the importance of using sanitary machinery parts in these industries and their role in ensuring optimal hygiene. Sanitary machinery parts are designed with smooth surfaces and seamless joints, eliminating areas where bacteria, allergens, or other contaminants can accumulate. Cross-contamination between batches or different products can be a significant concern in the food processing and pharmaceutical industry. By utilizing sanitary parts, the risk of cross-contamination is minimized, ensuring the purity and safety of the final products. Sanitary machinery parts are constructed using materials that are resistant to corrosion, easy to clean, and compatible with the cleaning agents used in these industries. They have smooth surfaces without cracks or crevices, making them easier to sanitize thoroughly. This reduces the potential for residue build-up, bacterial growth, and the formation of biofilms, which can compromise hygiene. Easy maintenance and cleaning procedures save time and resources while maintaining high cleanliness standards. Both the food processing and pharmaceutical industries are subject to stringent regulations and standards to ensure consumer safety. Regulatory bodies such as the FDA (Food and Drug Administration) and various global agencies impose strict guidelines on equipment and manufacturing practices. Using sanitary machinery parts demonstrates compliance with these regulations, safeguarding the reputation and integrity of the company and its products. Sanitary machinery parts play a crucial role in maintaining product quality and extending shelf life. The absence of contaminants ensures that the final products meet the desired specifications and are safe for consumption or use. By minimizing the risk of contamination from machinery parts, companies can provide consumers with products that meet or exceed quality expectations, contributing to customer satisfaction and loyalty. Microbial growth is a significant concern in the food processing and pharmaceutical industry. Sanitary machinery parts are designed to minimize the risk of microbial colonization by providing surfaces that are resistant to bacterial adhesion. This reduces the likelihood of contamination and microbial growth that could compromise product safety and stability. Using sanitary parts helps maintain the microbial control necessary to ensure the safety and efficacy of pharmaceuticals and the integrity of food products. In the event of a product recall or quality issue, traceability is crucial to identify the source of the problem and implement appropriate corrective actions. Sanitary machinery parts often come with unique identification codes or serial numbers, enabling easy traceability. This facilitates timely and targeted recalls, limiting the impact on consumers and minimizing financial losses for the company. In the food processing and pharmaceutical industry, maintaining optimal hygiene is paramount. Using sanitary machinery parts is an essential aspect of ensuring cleanliness, preventing cross-contamination, complying with regulations, enhancing product quality, and promoting consumer safety. By investing in sanitary components, companies can mitigate contamination risks, protect their brand reputation, and meet the demanding standards of these industries. Adopting these components demonstrates a commitment to hygiene and reinforces the confidence of consumers and regulatory bodies in the products manufactured. Certified hygienic components | Order | NHK Machinery Parts Hygienic conveyor parts in stainless steel | Order | NHK Machinery PartsSanitary Machinery Parts in the Food Processing and Pharmaceutical Industry
Preventing Cross-Contamination
Easy machinery parts to Clean and Maintain
Complying with Regulatory Standards
Enhancing Product Quality and Shelf Life
Preventing Microbial Growth
Ensuring Traceability and Recall Readiness
Hygienic Machinery Parts:
Ensuring Cleanliness and Safety in Food Processing and Pharmaceutical Industries