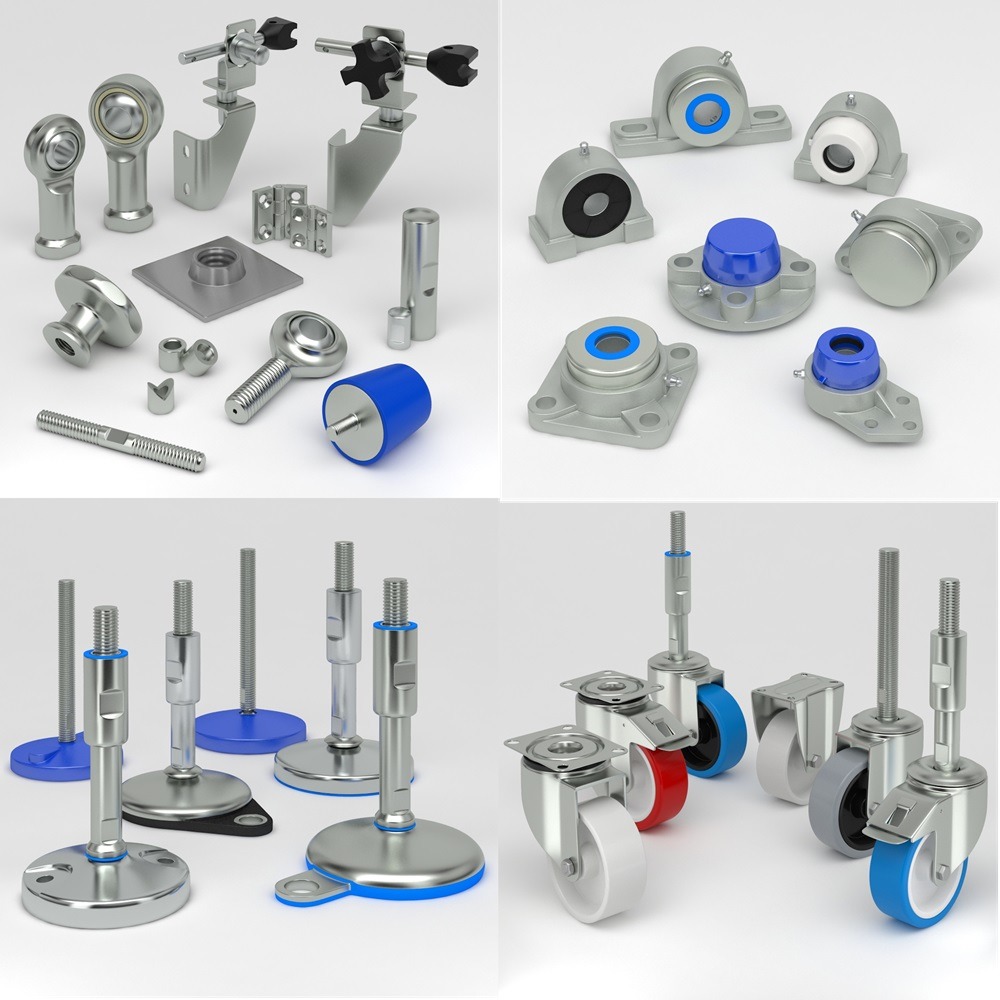
Pet Food Processing
The pet food industry has evolved significantly over the past decade. With pet owners becoming more conscious about the quality and safety of the food they provide to their furry friends, there is an increasing demand for high-quality pet food products. This growing awareness has also brought to light the importance of hygienic machinery components and sanitary conveyor parts in the pet food manufacturing process. For manufacturers, maintaining stringent hygiene standards is not just about meeting regulatory requirements but also about ensuring the safety and well-being of pets. In this article, we’ll explore the role of hygienic machinery components and sanitary conveyor parts in pet food processing, with a focus on applications, common equipment, and industry-specific considerations. Pet food processing involves handling a variety of raw materials, such as meat, grains, vegetables, and additives. This diverse ingredient mix makes pet food production susceptible to contamination if hygiene is not properly managed. Bacterial contaminants like Salmonella, E. coli, and Listeria pose a significant risk not only to pets but also to humans handling the food. To address these risks, equipment used in pet food processing must be designed with features that promote easy cleaning, minimize bacterial harborage points, and prevent cross-contamination. Hygienic machinery components, including bearings, seals, leveling feet, and enclosures, play a crucial role in maintaining these standards. Similarly, sanitary conveyor parts, such as belts, rollers, and support frames, must be designed with smooth surfaces and corrosion-resistant materials to prevent the build-up of residues and ensure the efficient transport of ingredients and finished products. The pet food industry encompasses a broad range of products, including dry kibble, wet canned food, semi-moist treats, and specialty diets. Each type of product requires specific processing techniques and equipment. Common applications include: Dry pet food, or kibble, is one of the most popular pet food formats. The production process involves several stages, including mixing, extrusion, drying, and coating. In this context, hygienic mixers and extruders are essential for ensuring uniform ingredient distribution and safe food output. Vacuum coaters are often used at the final stage to apply fat and flavor coatings to the kibble. Sanitary conveyor parts, such as smooth belts and rollers, ensure that kibble is transported safely between different production stages without contamination. Wet pet food is typically packed in cans, pouches, or trays and has a high moisture content. The production process involves grinding, mixing, cooking, and canning. Equipment such as mixers, vacuum fillers, and canning lines must be designed for easy disassembly and cleaning to avoid microbial growth. For wet pet food, it is crucial to use hygienic seals and gaskets in machinery to prevent leaks and contamination during high-temperature processes. Additionally, sanitary conveyor parts must be resistant to moisture and designed to drain easily to avoid water pooling. Specialty pet foods, including grain-free, organic, and limited ingredient diets, require even stricter hygiene standards. The processing of these diets often involves handling sensitive ingredients that can degrade or become contaminated easily. Therefore, hygienic machine components such as stainless-steel enclosures, food-grade lubricants, and IP67-rated waterproof bearings are recommended. Sanitary conveyors with modular belts allow quick dismantling and reconfiguration, making it easier to switch between different product lines without cross-contamination. The following equipment is commonly used in pet food manufacturing and is designed to meet hygiene standards: Extruders are used to shape dry and semi-moist pet foods. They work by forcing the mixture of ingredients through a die, which shapes the kibble. Hygienic extruders are designed with smooth, stainless-steel surfaces that are resistant to corrosion and allow for easy cleaning. Quick-release mechanisms and clean-in-place (CIP) systems enable efficient sanitation and reduced downtime during product changeovers. Mixers are used in the initial stages to blend various ingredients. In pet food processing, mixers must be designed with smooth, easy-to-clean surfaces, and their seals should prevent ingredient leakage. Hygienic design ensures that there are no dead zones where materials can accumulate and potentially harbor bacteria. Sanitary mixers often include removable shafts and paddles to facilitate thorough cleaning. Vacuum coaters are typically used in the final stage of dry pet food production to apply liquid fats, oils, and flavorings uniformly over the kibble. Vacuum coating improves the palatability and nutritional profile of the kibble. Hygienic vacuum coaters are designed with sloped surfaces and self-draining capabilities to prevent ingredient build-up. Wet pet food is often processed on canning lines, where the food is cooked and sealed in cans or pouches. The canning process involves high temperatures and pressure, making it crucial to use components that can withstand these conditions. Hygienic bearings and seals used in canning lines must be capable of withstanding heat and corrosion while maintaining tight seals to prevent leaks and contamination. When selecting hygienic machinery components and sanitary conveyor parts for pet food processing, manufacturers should consider the following: In the pet food processing industry, maintaining hygiene is of utmost importance to ensure product safety and quality. Hygienic machinery components and sanitary conveyor parts are integral to achieving these standards. By selecting components that promote ease of cleaning, prevent contamination, and withstand rigorous processing conditions, manufacturers can optimize their operations while delivering safe and high-quality pet food products. With the right equipment and processes in place, the pet food industry can continue to meet the growing demand for premium and specialty products that prioritize pet health and safety.
Hygienic Machinery Components and Sanitary Conveyor Parts for Pet Food Processing
The Importance of Hygiene in Pet Food Processing
Applications in Pet Food Processing
1. Production of Dry Pet Food
2. Production of Wet Pet Food
3. Production of Specialty Pet Foods
Common Equipment Used in Pet Food Processing
1. Extruders
2. Mixers
3. Vacuum Coaters
4. Canning Lines
Industry-Specific Considerations
Hygienic Machinery Components and Sanitary Conveyor Parts for Pet Food Processing
Contact
Articles