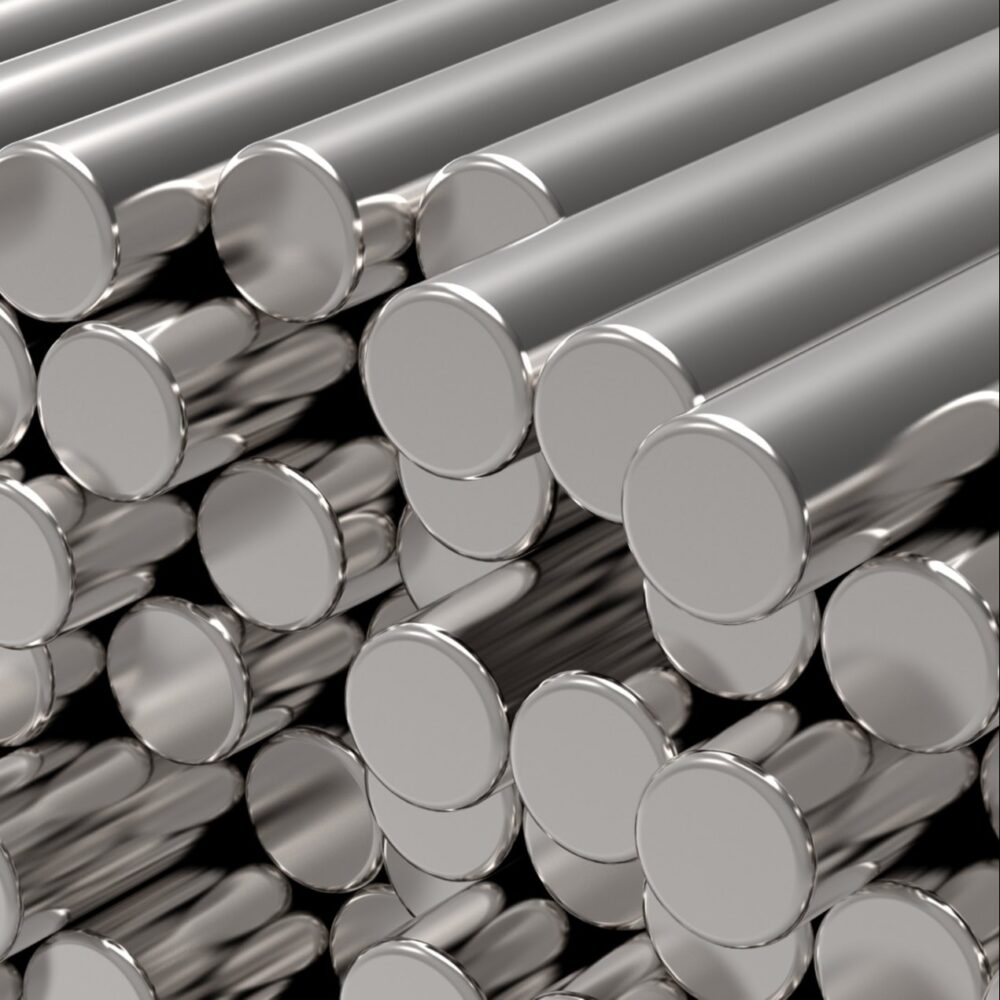
Next-Generation Stainless Steel: Revolutionizing Industries
In industries where hygiene, durability, and resistance to extreme environments are paramount, stainless steel has long been a material of choice. However, the emergence of next-generation stainless steel is revolutionizing operations across industries such as food processing, pharmaceuticals, biotechnology, and chemicals. This innovation offers enhanced properties that surpass conventional stainless steel grades, driving efficiency, safety, and sustainability. This article dives into the benefits of next-generation stainless steel and provides a comparison chart to help you understand its advantages in various industrial applications. Traditional stainless steel, including grades such as 304 and 316, has been a staple in industries that require hygiene and corrosion resistance. However, as industries face more rigorous standards and operational demands, the need for improved material performance has grown. Next-generation stainless steel addresses these challenges with advancements in: Next-generation stainless steel exhibits improved resistance to corrosion caused by chlorides, acids, and high moisture environments. This is critical in food processing where exposure to salts, acidic foods, and cleaning chemicals is common. With higher tensile strength and fatigue resistance, it can withstand extreme temperatures and physical stresses, making it ideal for equipment in biotechnology and pharmaceutical industries. The new alloys are designed for smoother finishes, minimizing crevices where contaminants can hide. This makes them perfect for industries with strict hygiene requirements, such as food and pharmaceutical production. Next-generation stainless steel is highly recyclable and energy-efficient during production, aligning with sustainability goals in chemical and biotechnology industries. Though the initial investment may be higher, the material’s longevity and low maintenance costs make it a cost-effective choice over time. In food processing, next-generation stainless steel is utilized in conveyors, storage tanks, and cutting equipment. Its corrosion resistance ensures safety when handling acidic foods and salty environments, while its hygienic properties minimize contamination risks. Pharmaceutical manufacturing relies on next-generation stainless steel for mixers, reaction vessels, and pipelines. Its ability to maintain integrity under high temperatures and its resistance to chemicals ensure safe and consistent production. Biotechnology applications require sterile environments. Next-generation stainless steel equipment meets stringent cleanability and durability standards, ensuring compatibility with bioprocessing technologies. Handling corrosive substances and high-pressure systems is routine in the chemical industry. Enhanced corrosion resistance and mechanical strength make next-generation stainless steel indispensable for chemical reactors and storage systems. For companies operating in competitive and regulated industries, upgrading to next-generation stainless steel isn’t just an option—it’s a necessity. Meeting regulatory standards, ensuring product safety, and optimizing operational efficiency are all achievable with this advanced material. Furthermore, industries like food processing and biotechnology are seeing increased demand for higher standards of cleanliness and durability, making the investment worthwhile. With advancements in alloy engineering, next-generation stainless steel continues to evolve. Future innovations are likely to focus on even greater resistance to extreme conditions, lighter-weight options, and enhanced sustainability. Industries at the forefront of technology adoption, like pharmaceuticals and biotechnology, are expected to drive these innovations further. Next-generation stainless steel represents a transformative step forward for industries such as food processing, pharmaceuticals, biotechnology, and chemicals. Its unparalleled properties, including enhanced corrosion resistance, durability, and hygienic compatibility, make it the material of choice for businesses striving for efficiency and compliance in challenging environments. By investing in this advanced material, companies can secure long-term benefits in operational efficiency, safety, and sustainability, ensuring they remain competitive in a rapidly evolving industrial landscape.
Next-Generation Stainless Steel: Revolutionizing Industries
Transforming Food Processing, Pharmaceutical, Biotechnology and Chemical Industries
Get our catalogue here
See our product line here
The Evolution of Stainless Steel
Key Benefits of Next-Generation Stainless Steel
1. Superior Corrosion Resistance
2. Enhanced Durability
3. Hygienic Design Compatibility
4. Sustainability
5. Cost Efficiency Over Time
Applications Across Industries
Food Processing
Pharmaceutical Industry
Biotechnology
Chemical Industry
Comparison Chart of Stainless Steel Grades
Grade
Corrosion Resistance
Durability
Hygienic Design
Cost
Best for
304 Stainless Steel
Moderate
Good
Basic
Affordable
General applications, low acidity
316 Stainless Steel
High
Very Good
Advanced
Higher
Food processing, pharmaceutical
Next-Gen Stainless
Excellent
Superior
Advanced+
Higher upfront
Extreme environments, long-term use
Why Upgrade to Next-Generation Stainless Steel?
The Future of Next-Generation Stainless Steel
Next-Generation Stainless Steel
Transforming Food Processing, Pharmaceutical, Biotechnology and Chemical Industries
Get our catalogue here
See our product line here
Contact
Articles