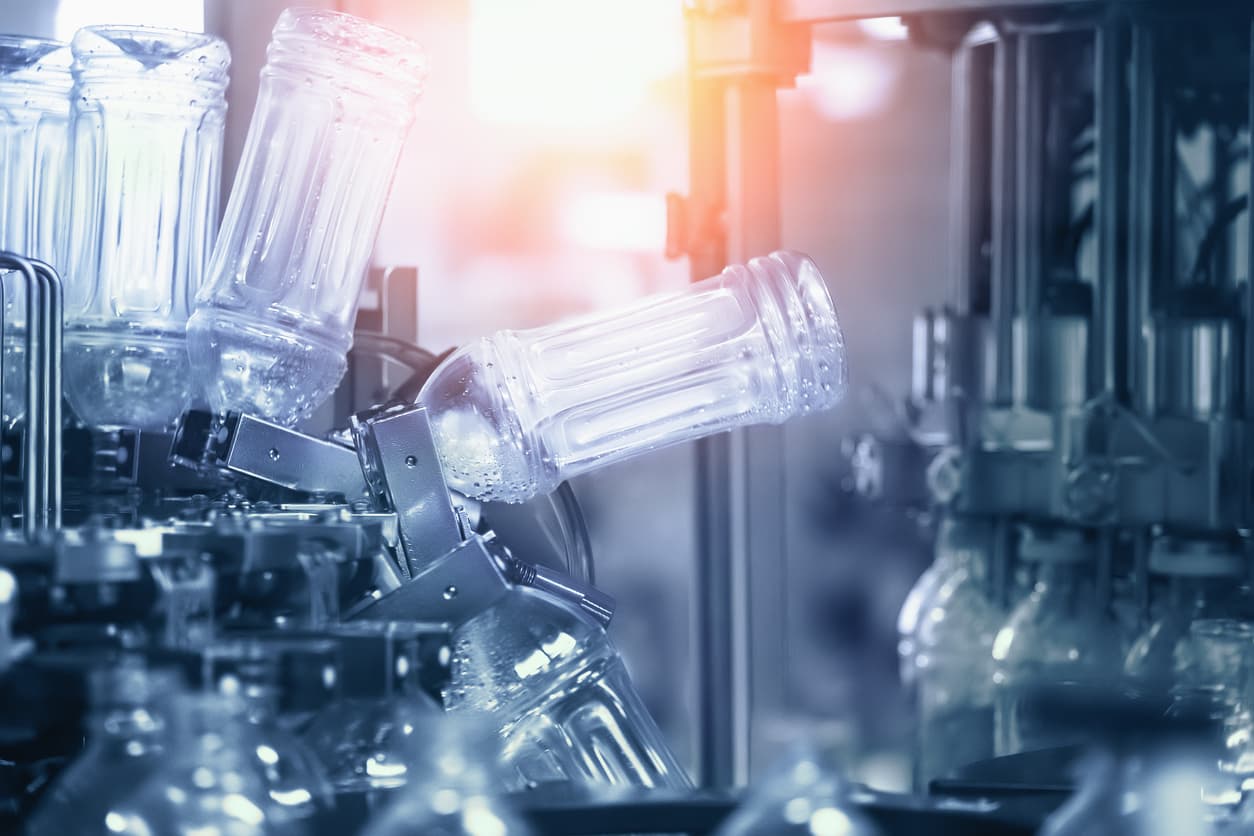
Keep the food processing running smoothly with proactive maintenance
Proactive maintenance is a vital aspect of keeping food processing operations running smoothly. By anticipating and fixing potential problems before they arise, manufacturers can avoid costly downtime, ensure food safety and maintain product quality. Here are some of the key benefits and best practices of proactive maintenance in the food processing industry. Downtime can be a major problem in food processing, as it not only affects productivity but can also impact the quality of the end product. By implementing a proactive maintenance program, manufacturers can identify and fix issues before they become serious, thus reducing the risk of unplanned downtime and maximizing uptime. Food safety is a top priority in the food processing industry. Proactive maintenance helps to ensure that equipment is functioning properly, which helps to reduce the risk of contamination. Additionally, regular maintenance helps to identify and address potential safety hazards, such as sharp edges on equipment or broken parts that could pose a risk to workers. Proactive maintenance can also help to ensure the quality of the end product by ensuring that equipment is functioning properly. For example, regular maintenance of refrigeration units can help to ensure that they are running efficiently and effectively, helping to prevent spoilage and maintain the quality of the food products. Proactive maintenance can also help to extend the life of equipment by identifying and fixing issues before they become serious. For example, by regularly checking and tightening belts, manufacturers can help to prevent belt failure, which can cause damage to other components and result in costly repairs. Proactive maintenance can also help to increase energy efficiency by identifying and fixing problems that can cause equipment to consume more energy. For example, regular cleaning of air filters can help to maintain proper air flow, which can reduce energy consumption and improve the efficiency of HVAC systems. Proactive maintenance is a critical component of a successful food processing operation. By reducing downtime, improving food safety, maintaining product quality, extending equipment life and increasing energy efficiency, proactive maintenance can help to ensure the success of a food processing operation. By following best practices, manufacturers can ensure that their operations run smoothly and that they are able to meet the demands of their customers. Certified hygienic components | Order | NHK Machinery Parts Hygienic conveyor parts in stainless steel | Order | NHK Machinery PartsProactive maintenance of food processing operations
Get our catalogue here
See our product line here
Minimize Downtime
Improve Food Safety
Maintain Product Quality
Extend Equipment Life
Increase Energy Efficiency
Best Practices for Proactive Maintenance
Successful food processing operation