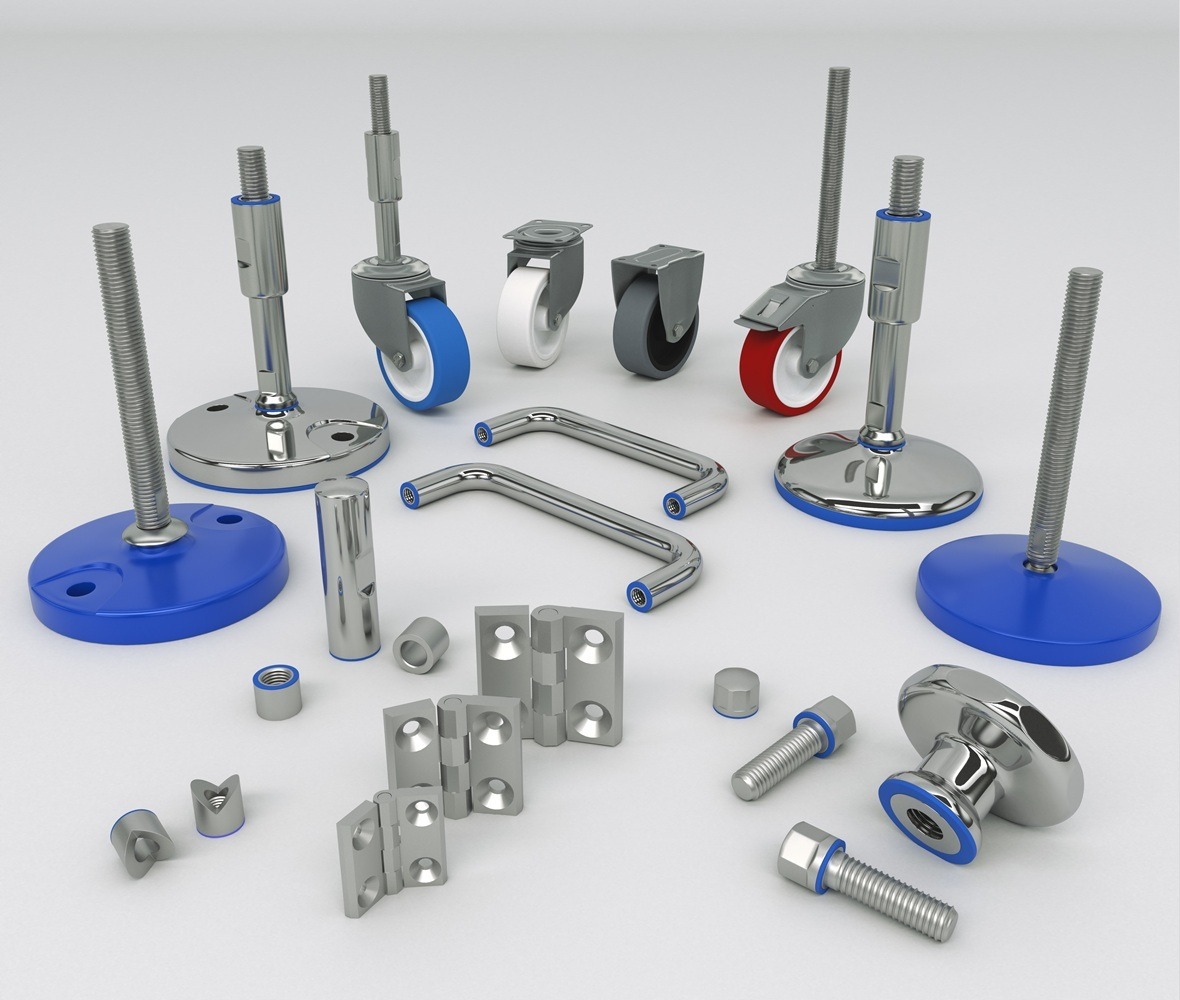
Hygienic Stainless Steel Components
In industries where hygiene is a top priority, such as food processing, pharmaceuticals, biotechnology, and personal care manufacturing, the choice of materials plays a crucial role in ensuring cleanliness, safety, and regulatory compliance. Stainless steel has emerged as the gold standard for hygienic components due to its durability, resistance to corrosion, and ease of cleaning. This article explores the importance of stainless steel hygienic components in the sanitary industry, their applications, and why they are essential for maintaining high hygiene standards. In the sanitary industry, maintaining impeccable hygiene standards is paramount. Central to achieving these standards is the use of hygienic components made from stainless steel. These components are designed to ensure cleanliness, prevent contamination, and comply with stringent regulatory requirements. Hygienic design refers to the engineering of equipment and components in a manner that facilitates easy cleaning and prevents the accumulation of contaminants. Stainless steel is the material of choice in this context due to its inherent properties: Stainless steel’s versatility makes it indispensable in various sanitary applications: Several stainless steel components are essential in maintaining hygiene in sanitary processes: Adherence to international standards ensures that stainless steel components meet the required hygiene and safety benchmarks: Proper maintenance and surface finishing of stainless steel components are vital for sustaining their hygienic properties: In the sanitary industry, the selection and maintenance of stainless steel hygienic components are critical to ensuring product safety and quality. By adhering to hygienic design principles, complying with international standards, and implementing proper maintenance protocols, industries can uphold the highest hygiene standards, safeguarding both consumers and products. Stainless steel offers several advantages that make it the ideal choice for sanitary applications: One of the primary reasons stainless steel is widely used in hygienic environments is its resistance to corrosion. The presence of chromium in stainless steel forms a passive oxide layer that protects the material from rust and deterioration, even in harsh cleaning and sterilization conditions. This ensures the longevity of components and reduces contamination risks. The non-porous and smooth surface of stainless steel prevents the accumulation of bacteria, dirt, and other contaminants. Unlike materials with microscopic crevices where microbes can hide, stainless steel ensures easy cleaning and sanitization, making it ideal for food processing, pharmaceutical, and medical applications. Stainless steel is highly durable and capable of withstanding extreme temperatures, mechanical stress, and aggressive cleaning processes involving high-pressure washing and chemical disinfectants. This makes it a cost-effective solution in industries where equipment is frequently cleaned and sanitized. Regulatory organizations such as the European Hygienic Engineering & Design Group (EHEDG), Sanitary Standards, and FDA (Food and Drug Administration) recommend stainless steel for applications requiring the highest hygiene standards. Its ability to comply with strict regulations ensures consumer safety and prevents contamination. Various stainless steel components are essential in maintaining hygiene in the sanitary industry. Here are some of the most important: Hygienic fittings, including clamps, couplings, and tri-clamp fittings, ensure leak-proof connections in sanitary processing lines. Stainless steel valves, such as butterfly and diaphragm valves, regulate fluid flow while maintaining high levels of hygiene. These components are designed for easy disassembly, cleaning, and sterilization. In food, pharmaceutical, and personal care industries, stainless steel conveyor belts and components are critical for safe product transportation. These conveyor parts are designed to meet hygienic standards, with features such as open-frame construction and easy-to-clean surfaces. Stainless steel tanks and mixing vessels are widely used in dairy, beverage, and pharmaceutical production. These vessels are resistant to contamination, easy to clean, and compatible with Clean-in-Place (CIP) and Sterilize-in-Place (SIP) systems, ensuring product purity. Hygienic stainless steel leveling feet are essential for stabilizing machinery in sanitary environments. Designed with smooth surfaces and minimal crevices, they prevent the accumulation of dirt and bacteria. Some models include self-draining features to avoid water retention, enhancing hygiene. Bearings and housings made from stainless steel are resistant to corrosion and contamination. IP67/IP69-rated waterproof bearings ensure protection against moisture and harsh cleaning chemicals, making them suitable for hygienic environments. Stainless steel hygienic components are used in various industries where cleanliness and product safety are critical. Ensuring compliance with hygiene standards is critical in the sanitary industry. The most recognized certifications and standards for stainless steel components include: Regular cleaning and maintenance of stainless steel components are necessary to uphold hygiene standards and extend the lifespan of equipment. Avoid abrasive cleaners and use recommended sanitizers such as alkaline detergents and peracetic acid-based disinfectants. This prevents damage to the stainless steel’s passive layer. CIP and SIP systems automate the cleaning process, ensuring that stainless steel components are thoroughly cleaned without disassembly, reducing downtime. Regularly inspect hygienic components for wear, corrosion, or damage. Replace any worn-out parts immediately to prevent contamination risks. Electropolishing further enhances the corrosion resistance and cleanliness of stainless steel surfaces, reducing bacterial adhesion and making cleaning more effective. Hygienic stainless steel components are the backbone of the sanitary industry, ensuring compliance with strict hygiene standards and safeguarding product integrity. Their corrosion resistance, smooth surfaces, and high durability make them indispensable in food processing, pharmaceuticals, cosmetics, and chemical industries. By choosing high-quality stainless steel components and following best practices for maintenance, businesses can enhance hygiene, improve efficiency, and meet industry regulations. For organizations looking to invest in reliable hygienic stainless steel components, working with certified suppliers who adhere to global sanitary standards is crucial. Stainless steel will continue to be a cornerstone in the pursuit of hygienic excellence, ensuring the safety and quality of products in the sanitary industry.
The Role of Hygienic Stainless Steel Components in the Sanitary Industry
The Crucial Role of Hygienic Stainless Steel Components in the Sanitary Industry
Ensuring Cleanliness, Safety and Compliance
The Importance of Hygienic Design
Applications in the Sanitary Industry
Key Hygienic Components
Standards and Compliance
Maintenance and Surface Finishing
Why Stainless Steel is the Preferred Choice for Hygienic Applications
1. Corrosion Resistance
2. Smooth and Non-Porous Surface
3. High Durability and Strength
4. Compliance with Hygienic Standards
Key Hygienic Components in Stainless Steel
1. Stainless Steel Hygienic Fittings and Valves
2. Stainless Steel Conveyor Components
3. Stainless Steel Tanks and Vessels
4. Stainless Steel Machine Leveling Feet
5. Stainless Steel Bearings and Housings
Applications of Hygienic Stainless Steel Components
1. Food and Beverage Industry
2. Pharmaceutical and Biotechnology Industry
3. Cosmetics and Personal Care Industry
4. Chemical and Cleaning Products Industry
Standards and Certifications for Stainless Steel Hygienic Components
Best Practices for Cleaning and Maintaining Stainless Steel Hygienic Components
1. Use Proper Cleaning Agents
2. Implement Clean-in-Place (CIP) and Sterilize-in-Place (SIP) Systems
3. Conduct Routine Inspections
4. Use Electropolished Stainless Steel Surfaces
Hygienic Stainless Steel Components: The Key to Sanitary Industry Excellence
Contact
Articles