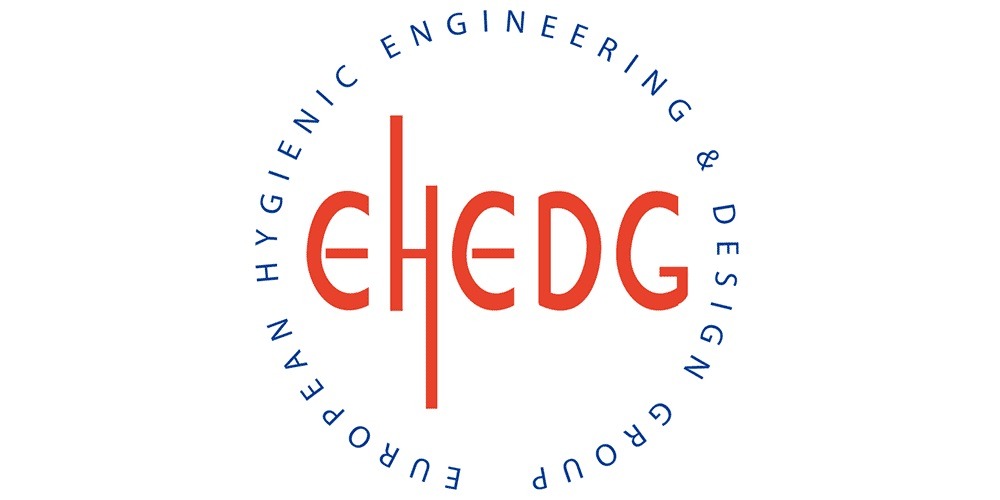
How to Get EHEDG Certified: A Comprehensive Guide
Obtaining an EHEDG (European Hygienic Engineering and Design Group) certification is a crucial step for businesses in the food processing, pharmaceutical, and biotechnology industries. This certification ensures that equipment and processes meet the highest standards of hygiene and safety. In this guide, we’ll walk you through the process of getting EHEDG certified, from understanding the requirements to successfully passing the certification audit. Additionally, we’ll explore four case studies to illustrate the journey of different companies towards achieving this prestigious certification. EHEDG certification is a testament to the hygienic design of equipment and facilities used in the production of food, pharmaceuticals, and other sensitive products. It ensures that the equipment is easy to clean, prevents contamination, and complies with stringent European standards. EHEDG certification is important for several reasons: Begin with an initial assessment to understand where your equipment and processes stand concerning EHEDG standards. Conduct a gap analysis to identify areas that need improvement. Based on the gap analysis, make necessary design and engineering adjustments. This may involve redesigning equipment to meet hygienic standards, ensuring easy cleanability, and using appropriate materials. Prepare detailed documentation of your processes, materials used, and design changes. Implement the necessary changes and ensure that all procedures align with EHEDG guidelines. Conduct an internal audit to ensure all changes meet EHEDG standards. A pre-assessment by an EHEDG-approved auditor can provide valuable insights and help identify any remaining issues. Submit your application for an official EHEDG audit. An auditor will visit your facility, review documentation, and inspect equipment to ensure compliance. If your facility passes the audit, you will receive EHEDG certification. It’s important to maintain standards and continually improve processes to retain the certification. Company Overview: A large dairy processing plant aimed to enhance its hygiene standards and gain access to European markets. Challenges: The plant had outdated equipment and lacked proper documentation. Solution: The company conducted a thorough gap analysis, redesigned equipment to meet EHEDG standards, and implemented a robust documentation system. After a successful internal audit, they passed the official EHEDG audit. Result: The plant achieved EHEDG certification, which led to increased market access and improved product safety. Company Overview: A pharmaceutical manufacturing unit wanted to ensure its equipment met the highest hygiene standards. Challenges: The facility had complex equipment that was difficult to clean. Solution: The company invested in new equipment designed according to EHEDG guidelines and trained staff on proper cleaning procedures. Documentation was meticulously prepared, and a pre-assessment identified minor issues that were quickly resolved. Result: The unit achieved EHEDG certification, enhancing its reputation and ensuring compliance with European standards. Company Overview: A mid-sized food processing facility sought EHEDG certification to improve hygiene and safety standards. Challenges: The facility had inconsistent cleaning procedures and lacked comprehensive documentation. Solution: The company standardized its cleaning procedures, upgraded equipment, and developed detailed documentation. An internal audit followed by a pre-assessment helped identify and rectify any issues. Result: The facility successfully achieved EHEDG certification, leading to safer products and increased customer trust. Company Overview: A biotechnology firm needed EHEDG certification to comply with industry regulations and expand its market. Challenges: The firm faced challenges with equipment cleanability and material compatibility. Solution: The firm worked closely with EHEDG consultants to redesign equipment and select appropriate materials. Extensive staff training and rigorous internal audits ensured compliance. Result: The firm achieved EHEDG certification, facilitating market expansion and ensuring high standards of hygiene and safety. Achieving EHEDG certification is a multifaceted process that requires careful planning, design adjustments, and rigorous auditing. By following the steps outlined in this guide and learning from the case studies, businesses can successfully navigate the certification process and reap the benefits of enhanced hygiene, safety, and market access.
EHEDG certification is a crucial step
What is EHEDG Certification?
Why is EHEDG Certification Important?
Steps to Achieve EHEDG Certification
Step 1: Initial Assessment and Gap Analysis
Step 2: Design and Engineering Adjustments
Step 3: Documentation and Implementation
Step 4: Internal Audit and Pre-Assessment
Step 5: Official EHEDG Audit
Step 6: Certification and Continuous Improvement
Case Studies
Case Study 1: Dairy Processing Plant
Case Study 2: Pharmaceutical Manufacturing Unit
Case Study 3: Food Processing Facility
Case Study 4: Biotechnology Firm
EHEDG Certified 3a ssi standard components | Order | NHK Machinery Parts
Contact
Articles