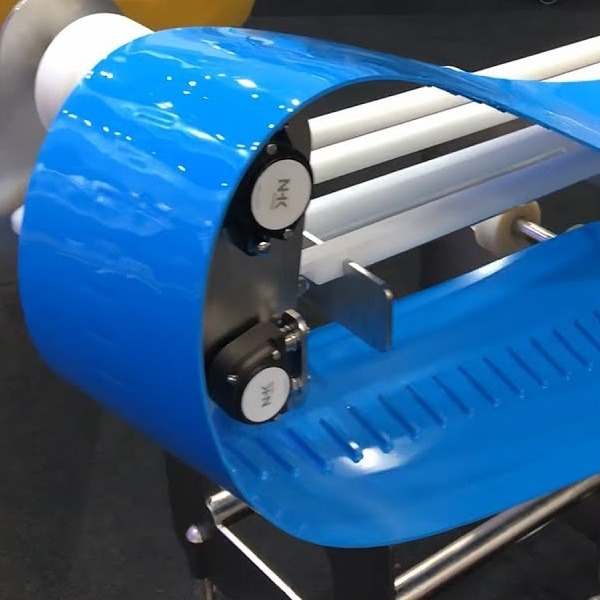
Ease to Clean VS Maintenance Accessibility
In modern production environments, particularly in the food, pharmaceutical, and biotechnology industries, machine design plays a pivotal role in ensuring operational efficiency and regulatory compliance. Accessibility for maintenance and ease of cleaning have become essential design considerations for manufacturers of machinery components such as hygienic leveling feet, IP67 waterproof bearing units, and easy-to-remove conveyor belts. This dual focus on cleaning and maintenance accessibility not only safeguards product quality but also minimizes downtime, reduces costs, and enhances overall productivity. Ensuring ease of cleaning is fundamental to maintaining hygienic processing environments. The design of machinery and its components can significantly influence how quickly and thoroughly cleaning can be accomplished. Features like tool-free disassembly and smooth, residue-repellent surfaces prevent product buildup and bacterial contamination. The ability to disassemble machinery without specialized tools drastically reduces the time required for cleaning. Components that can be easily detached, such as modular conveyor belts or quick-release bearing housings, empower workers to access hard-to-reach areas without disrupting production schedules. This feature also reduces the risk of improper reassembly, thereby supporting a safer production environment. Smooth surfaces, rounded edges, and the elimination of crevices or hard-to-reach areas prevent the accumulation of dust, debris, and product residue. Crevices are notorious for harboring bacteria and contaminants that are difficult to clean. By employing crevice-free designs, machinery manufacturers align with stringent regulatory requirements, such as those set by the Food and Drug Administration (FDA) and the European Hygienic Engineering and Design Group (EHEDG). Stainless steel, particularly AISI 304 and 316 grades, is a preferred material for hygienic machine components. Its non-porous nature, resistance to corrosion, and ability to withstand repeated washdowns make it ideal for food, pharmaceutical, and biotechnology environments. Additionally, anti-microbial coatings can be applied to further enhance the surface’s resistance to bacterial growth. Components like conveyor belts, hygienic leveling feet, and mounting brackets are often designed with sloped surfaces to promote liquid drainage during washdowns. By facilitating drainage, these components prevent the pooling of water, which could lead to bacterial growth. Drainage-friendly design reduces drying time and accelerates the overall cleaning process. While ease of cleaning focuses on hygiene, maintenance accessibility ensures that machine operators and technicians can quickly access critical components for repairs, adjustments, or replacements. Components designed with maintenance accessibility in mind minimize downtime and ensure uninterrupted production. Hygienic leveling feet play a dual role in supporting the machine’s stability and enabling easy cleaning. These feet are typically made from stainless steel, are height-adjustable, and feature smooth, self-draining surfaces. Some leveling feet include vibration-damping properties, further supporting production stability. When maintenance is required, these leveling feet can be quickly adjusted, disassembled, or replaced without requiring specialized tools. Conveyor belts are one of the most critical components in continuous production processes. For maintenance purposes, belts must be easily removable to facilitate quick replacements or repairs. Modular conveyor belts with quick-release mechanisms allow operators to swap out damaged sections or belts with minimal disruption. Additionally, belts made from hygienic, food-grade materials like polypropylene or polyethylene are often designed with detachable links, which allows for localized replacement instead of full belt replacement. Bearings are essential for the smooth movement of conveyor systems and rotating machinery. However, exposure to moisture, cleaning agents, and high-pressure washdowns can compromise their integrity. IP67 waterproof bearing units are specifically designed to endure extreme environments. They feature fully sealed housings that prevent water, dust, and contaminants from entering. In addition, many IP67 bearings come with pre-lubricated and maintenance-free designs, further minimizing downtime. Another innovation supporting maintenance accessibility is the use of color-coded components. These visual cues allow operators and maintenance teams to quickly identify which parts are intended for cleaning, maintenance, or replacement. For example, components requiring frequent inspection may be color-coded red, while non-critical components are coded blue or green. This simple but effective design strategy significantly improves the speed and efficiency of maintenance activities. While ease of cleaning and maintenance accessibility are often viewed as separate design goals, they are inherently interconnected. Both objectives aim to maximize machine uptime, reduce labor costs, and maintain hygienic conditions. For example, tool-free disassembly benefits both cleaning and maintenance activities. Hygienic leveling feet support sanitary conditions while also allowing for quick machine adjustments or relocations. Moreover, regulatory standards such as the FDA’s Current Good Manufacturing Practices (cGMP) and EHEDG guidelines emphasize both hygiene and ease of maintenance. Machines that meet these standards ensure compliance, enhance brand reputation, and mitigate the risk of costly product recalls. Implementing design principles that prioritize accessibility and cleaning ease delivers several operational advantages: The principles of accessibility and cleaning ease are essential in the following industries: Incorporating design principles that prioritize ease of cleaning and maintenance accessibility offers numerous operational benefits. Tool-free disassembly, smooth surfaces, and crevice-free components reduce cleaning time and enhance regulatory compliance. Simultaneously, accessible hygienic leveling feet, removable conveyor belts, and IP67 waterproof bearing units enable efficient maintenance, minimizing production downtime. Industries like food processing, pharmaceuticals, and biotechnology depend on these principles to maintain competitive advantages and meet strict hygiene regulations. By focusing on both accessibility and ease of cleaning, manufacturers and production facilities can achieve higher productivity, lower operating costs, and uncompromising hygiene standards. Investing in advanced machine design that supports these goals is not just a good business decision—it’s a strategic imperative for sustained growth and regulatory compliance.
Design for Accessibility and Cleaning: The Cornerstone of Hygienic Machine Design
Ease of Cleaning and Maintenance
1. Tool-Free Disassembly
2. Smooth Surfaces and Crevice-Free Design
3. Hygienic Materials and Coatings
4. Sloped Design for Drainage
Maintenance Accessibility
1. Hygienic Leveling Feet
2. Easy-to-Remove Conveyor Belts
3. IP67 Waterproof Bearing Units
4. Color-Coded Components for Quick Identification
The Synergy Between Cleaning and Maintenance Accessibility
Benefits of Accessible and Easy-to-Clean Machine Design
Industry Applications
Incorporating design principles
Contact
Articles