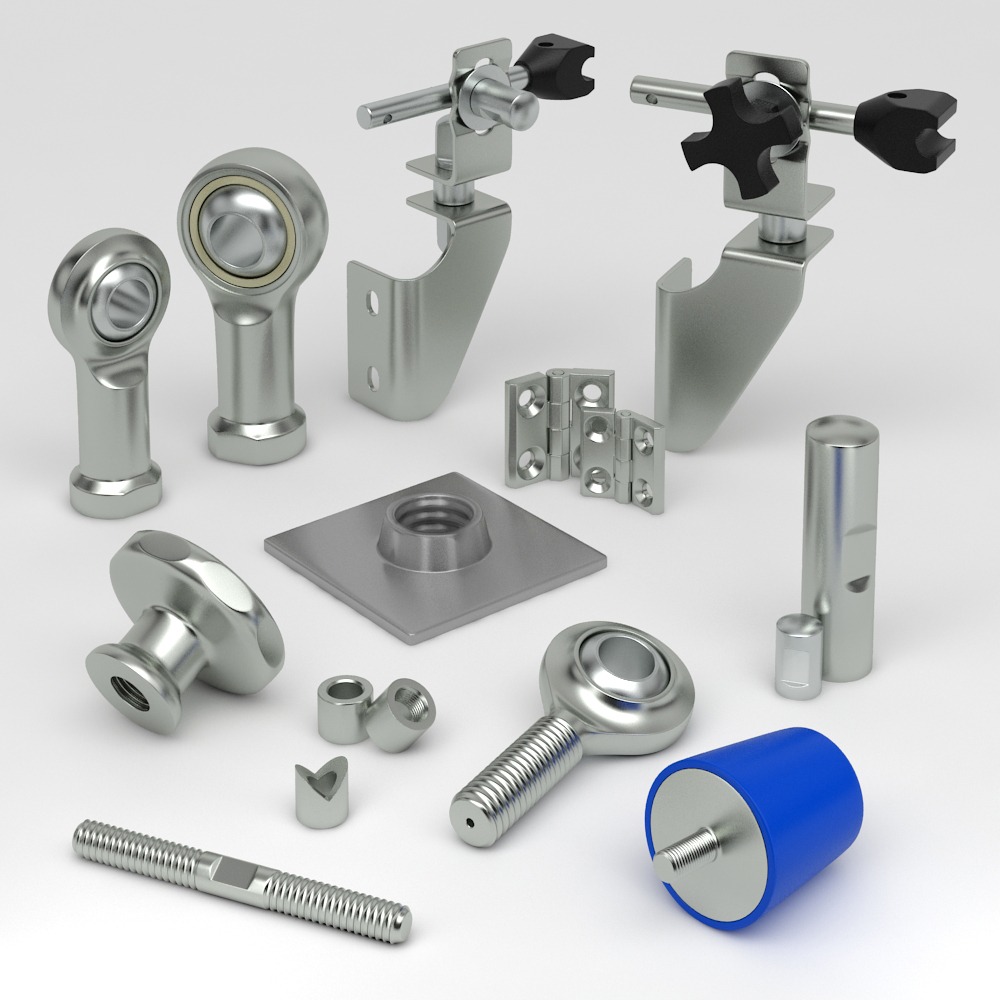
Dairy Processing
The dairy processing industry is a cornerstone of the global food sector, producing essential products such as milk, cheese, yogurt, butter, and ice cream. As consumer demand for high-quality and safe dairy products grows, maintaining strict hygiene and sanitation standards in dairy production has become more critical than ever. Achieving this requires the use of hygienic machinery components and sanitary conveyor parts specifically designed for the unique challenges of dairy processing. These components not only ensure product safety and compliance with industry regulations but also enhance production efficiency and minimize the risk of contamination. Dairy processing involves complex procedures, such as pasteurization, homogenization, and fermentation, that require precise control and rigorous cleanliness. Any deviation in hygiene can result in contamination, leading to spoilage and health risks. As a result, the equipment used in dairy production must be constructed to meet stringent sanitary standards, such as those set by the FDA, EHEDG, and 3-A SSI. Hygienic machinery components and sanitary conveyor parts are engineered to withstand these high standards while maintaining durability, functionality, and ease of cleaning. Hygienic components are designed to comply with food safety standards, such as FDA, EHEDG, and 3-A SSI. These regulations specify requirements for materials, surface finishes, and design to minimize the risk of contamination. Components such as hygienic bearings, leveling feet, and seals are made from food-grade stainless steel and other non-toxic materials that are easy to clean and resistant to corrosion. One of the main concerns in dairy processing is bacterial growth in hard-to-clean areas. Hygienic machinery components feature smooth surfaces, rounded edges, and sealed joints to eliminate gaps and crevices where bacteria can accumulate. Sanitary conveyor parts are designed with open frames and easy-to-remove belts, allowing for thorough cleaning and inspection. Dairy processing environments are harsh, with frequent exposure to water, cleaning chemicals, and varying temperatures. Hygienic components are built to withstand these conditions, ensuring reliable performance over long periods. IP67-rated bearings and corrosion-resistant fasteners are examples of components designed for durability in wet and washdown environments, minimizing maintenance and downtime. Conveyors are essential in dairy processing for transporting products between different stages of production, such as from the pasteurizer to the filling station. Sanitary conveyor parts are specifically designed to prevent contamination and ensure smooth product handling. Key considerations for these conveyors include: When selecting hygienic machinery components and sanitary conveyor parts for dairy processing, several factors should be considered: Hygienic machinery components and sanitary conveyor parts are vital for ensuring the safety, quality, and efficiency of dairy processing operations. From milk and cheese to yogurt and ice cream, these components play a crucial role in maintaining strict hygiene standards and optimizing production. By investing in high-quality, compliant hygienic components, dairy processors can protect their products, meet regulatory requirements, and deliver safe and delicious dairy products to consumers around the world.
The Essential Role of Hygienic Machinery Components and Sanitary Conveyor Parts in Dairy Processing
The Unique Challenges of Dairy Processing
Key Applications in Dairy Processing
The Importance of Hygienic Machinery Components in Dairy Processing
1. Compliance with Food Safety Regulations
2. Resistance to Bacterial Growth
3. Enhanced Durability and Performance
The Role of Sanitary Conveyor Parts in Dairy Processing
Choosing the Right Hygienic Components for Dairy Processing
The Essential Role of Hygienic Machinery Components and Sanitary Conveyor Parts in Dairy Processing
Contact
Articles