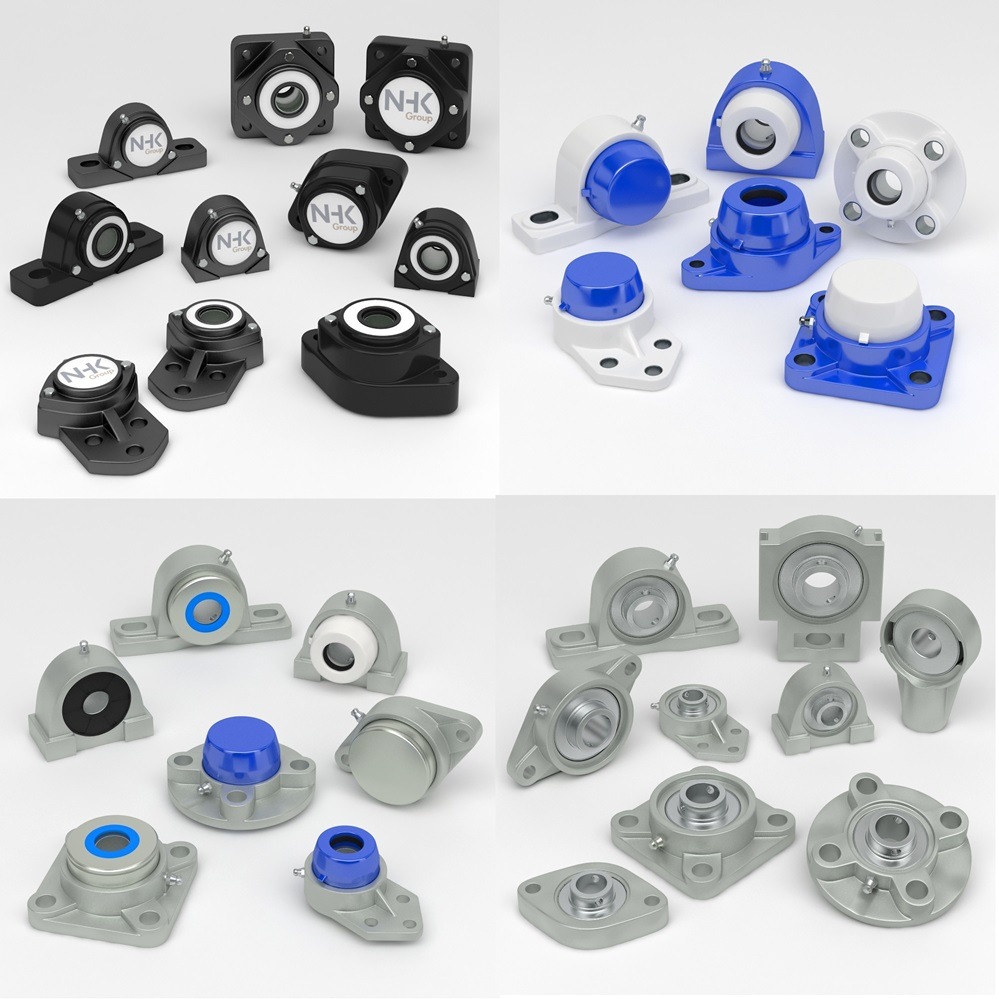
Convenience Food Processing
The convenience food processing industry is thriving as consumer demand for ready-to-eat meals, instant soups, and microwaveable snacks continues to grow. With busy lifestyles driving the need for quick and easy meal solutions, manufacturers in the sector are constantly innovating to deliver high-quality, safe, and appealing food products. Central to this effort are the hygienic machinery components and sanitary conveyor parts that ensure food safety, efficiency, and compliance with industry standards. Convenience food processing involves a range of products such as ready-to-eat meals, microwaveable snacks, and instant soups. The manufacturing process is complex, requiring specialized equipment like mixing machines, forming equipment, cooking systems, and advanced packaging machinery. This variety of machinery plays a crucial role in handling various food ingredients and ensuring that products are processed under strict hygienic conditions. Hygienic machinery components and sanitary conveyor parts are essential for maintaining the quality and safety of these food products. They help prevent contamination, simplify cleaning processes, and support compliance with global food safety standards, such as the FDA (Food and Drug Administration) and EHEDG (European Hygienic Engineering & Design Group) guidelines. Hygienic components are specifically designed to meet the strict hygiene requirements of food processing environments. They include elements such as stainless steel bearings, seals, leveling feet, and machine housings that come into direct or indirect contact with food products. Here’s why they are vital in convenience food processing: Sanitary conveyor systems are integral to the efficiency and safety of convenience food production. These systems transport raw ingredients, semi-finished products, and finished items throughout the processing plant. Key sanitary conveyor parts include belts, rollers, bearings, and guides, all of which are designed for ease of cleaning and resistance to food residues and contaminants. Hygienic components and sanitary conveyor parts play a significant role in various stages of convenience food processing. Here’s a closer look at their applications: Recent innovations in the field have focused on creating equipment that not only meets but exceeds hygiene standards. This includes self-draining surfaces, minimal contact points, and enhanced sealing technologies. Manufacturers are also increasingly turning to automation and robotics to reduce human contact and potential contamination risks. Another trend is the use of antimicrobial materials in machine components and conveyor belts. These materials inhibit the growth of bacteria and other microorganisms, providing an additional layer of protection. For example, antimicrobial conveyor belts used in packaging machines for instant soups can help maintain hygiene during extended production runs. The convenience food processing industry relies heavily on hygienic machinery components and sanitary conveyor parts to deliver high-quality, safe, and appealing food products. From mixing machines to packaging systems, every piece of equipment must be designed with hygiene in mind to meet the stringent requirements of this fast-growing sector. By investing in hygienic and sanitary components, manufacturers can ensure product safety, comply with global standards, and optimize production efficiency. As consumer demand for convenience foods continues to rise, the role of these components will only become more critical in shaping the future of food processing.
The Role of Hygienic Machinery Components and Sanitary Conveyor Parts in Convenience Food Processing
Understanding Convenience Food Processing
Importance of Hygienic Machinery Components
Role of Sanitary Conveyor Parts in Convenience Food Processing
Key Applications in Convenience Food Processing
Innovations in Hygienic Design
EHEDG and 3-A SSI standard certified components
Contact
Articles