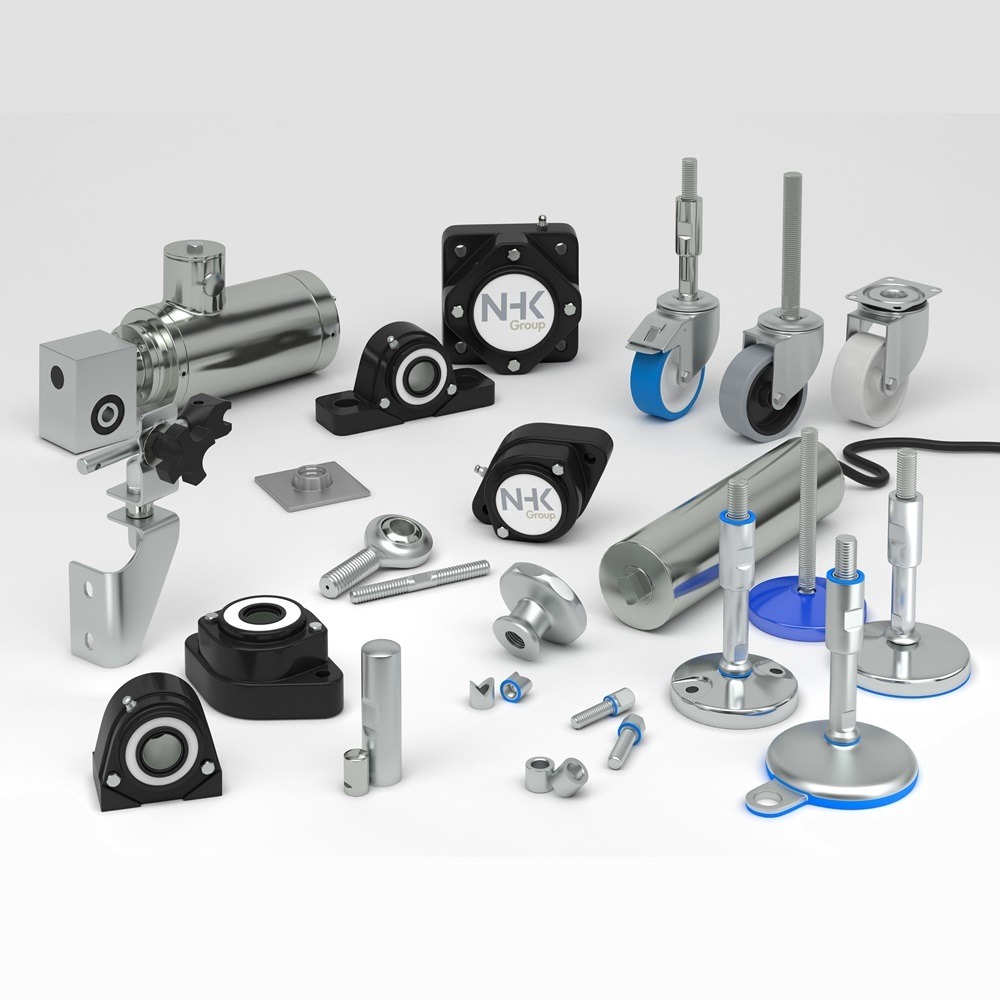
Certified Hygienic Components
In today’s fast-paced manufacturing environments, especially in sectors like food processing, pharmaceuticals, cosmetics, and biotechnology, hygiene is non-negotiable. One minor contamination incident can escalate into a full-blown product recall, damaging brand reputation, causing financial losses, and endangering public health. The foundation of contamination control begins with certified industrial machinery parts and hygienic components that are specifically designed for easy cleaning, resistance to bacteria, and compliance with global hygiene standards. Industrial machines are only as safe as their weakest component. Poorly designed or uncertified parts often harbor bacteria in hard-to-reach areas, corrode easily, or degrade under harsh cleaning procedures. These weaknesses can lead to: Biofilm formation in joints, gaps, and seals. Cross-contamination between batches or product lines. Equipment malfunction due to wear or corrosion. Violation of hygiene standards, leading to audits, fines, or shutdowns. For industries dealing with consumables or sensitive pharmaceuticals, these issues can quickly spiral into expensive product recalls. Certified hygienic components are engineered for use in environments where cleanliness is paramount. These include: Stainless steel machine leveling feet IP67/IP69K waterproof bearing units EHEDG certified knobs, handles, and fasteners Sealed caster wheels for cleanroom environments FDA-approved gaskets and seals Each component undergoes rigorous design and testing to meet hygiene regulations from EHEDG, FDA, and ISO 14159. Certification ensures that components resist contamination, are easy to clean, and do not deteriorate under chemical or thermal exposure. Certified hygienic components incorporate design features that actively reduce contamination risks: A rough or porous surface promotes microbial adhesion. Certified components feature Ra<0.8 µm surface finishes, often polished to a mirror-like state, to prevent biofilm buildup and allow for easy cleaning. Hygienic components are designed without horizontal surfaces or blind spots. Self-draining geometries allow cleaning fluids and water to easily flow off, reducing the risk of standing liquid, which could become a contamination source. Gaps, threads, or crevices are breeding grounds for bacteria. Certified machinery parts are equipped with sealed joints, encapsulated fasteners, and non-threaded designs to eliminate entry points for contaminants. High-grade stainless steel (AISI 316L or better) is used due to its corrosion resistance and compatibility with aggressive cleaning agents, steam, and high temperatures. Elastomers used in seals and gaskets are FDA-approved and compliant with food contact regulations. Product recalls are devastating. Whether it’s due to salmonella in meat processing or contamination in a pharmaceutical batch, the damage is swift and widespread. According to the FDA and EFSA, over 60% of recalls in food and drug industries are linked to equipment hygiene failures. Hygienic components help prevent these costly events by: Ensuring CIP (Clean-In-Place) compatibility Eliminating areas where bacteria or allergens may linger Reducing downtime through easy disassembly and cleaning Providing traceability through part certification and serial coding Hygienic machine components are essential in food production—from dairy to baked goods. Certified machine feet, sealed bearings, and FDA-compliant conveyor parts reduce the risk of listeria, salmonella, and allergen cross-contamination. Cleanrooms and sterile production zones require components with IP67/IP69K waterproof ratings and EHEDG approval to maintain aseptic conditions. Certified stainless knobs, casters, and adjustable feet allow for precise setup without compromising hygiene. In the cosmetics industry, maintaining product purity is crucial. Hygienic components protect creams, gels, and serums from microbial contamination while complying with GMP and ISO standards. Filling lines, pasteurizers, and bottling equipment benefit from hygienic design to prevent mold or yeast formation in valves, joints, and bearings. Investing in certified hygienic parts is more cost-effective than managing the fallout of a contamination incident. Consider these costs associated with a product recall: Logistics and recall handling Legal fees and settlements Regulatory fines Loss of customer trust Production downtime By contrast, hygienic components may carry a slightly higher upfront cost but provide long-term savings through reduced maintenance, faster cleaning, fewer inspections, and most importantly, peace of mind. When selecting components, always ask for documentation and certification from recognized organizations: EHEDG (European Hygienic Engineering and Design Group) Sanitary Standards (U.S. dairy and food equipment) FDA compliance for food-contact materials NSF certification for cleanability and corrosion resistance ISO 14159: Safety of machinery – Hygiene requirements Suppliers who provide full documentation, traceability, and testing results should always be prioritized. Choosing the right supplier is just as important as selecting the right component. Look for: Specialization in hygienic and sanitary components Transparent certification and testing protocols Custom engineering support for your specific application Stock availability and lead time transparency Commitment to sustainability and compliance Reputable manufacturers like NHK Machinery Parts, NHK Hygienic Components and NHK Group offer a wide range of certified hygienic components tailored to food, pharma, and biotech operations. In industries where contamination control is paramount, it’s no longer sufficient to retrofit or sanitize existing systems. Hygiene must be built into the foundation—starting with every bolt, foot, knob, and bearing. Certified industrial machinery parts and hygienic components are not just an option—they are a necessity for companies committed to quality, safety, and brand integrity. They safeguard your process, your product, and most importantly, your reputation.
Why Hygiene Matters in Industrial Machinery
The Hidden Risks of Uncertified or Outdated Machinery Parts
Certified Hygienic Components: The First Line of Defense
Avoiding Contamination: Design Features that Matter
1. Smooth Surface Finishes
2. Self-Draining Geometry
3. Sealed Interfaces
4. Material Resistance
The Role of Hygienic Design in Preventing Product Recalls
Industries That Benefit from Certified Hygienic Components
Food Processing
Pharmaceuticals and Biotechnology
Cosmetics and Personal Care
Beverage Industry
Cost Benefits: Prevention Is Cheaper Than a Recall
Certification Standards to Look For
Smart Purchasing Decisions: What to Look for in a Supplier
Build Hygiene Into the Foundation
Contact
Articles