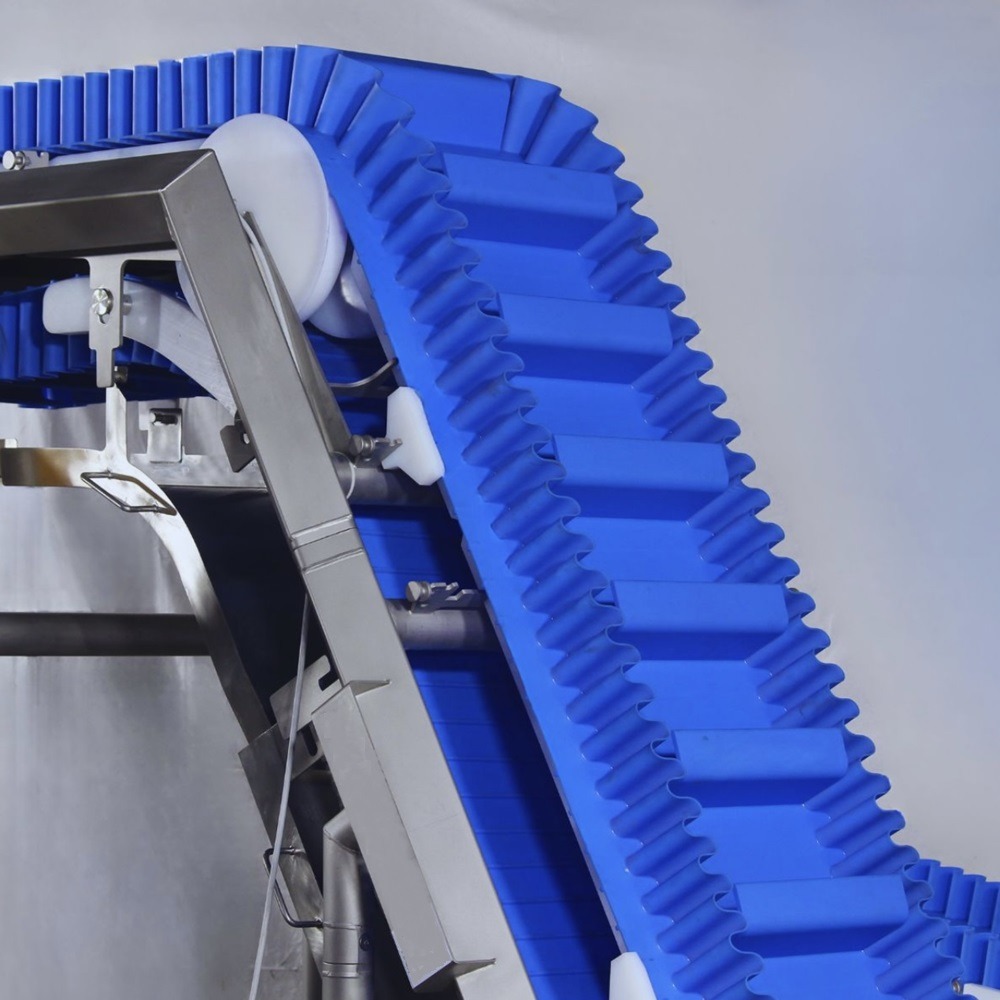
Cereal and Grain Processing
The cereal and grain processing industry is a cornerstone of the global food market, producing staple foods such as breakfast cereals, flour, pasta, and grain-based snacks. Given the large scale and high-speed nature of these production lines, maintaining the highest hygiene standards is essential. From raw grain intake to finished product packaging, every stage must ensure food safety, prevent contamination, and comply with stringent hygiene regulations. Hygienic machinery components and sanitary conveyor parts play a critical role in ensuring food safety in cereal and grain processing. Since products like flour and cereals are susceptible to contamination and spoilage, it is crucial to use machinery designed to minimize bacterial buildup and facilitate easy cleaning. Hygienic components are more than just a regulatory requirement; they are an investment in product quality and plant efficiency. Below are some essential hygienic components and their role in cereal and grain processing: The cereal and grain industry faces several unique hygiene challenges, primarily related to dust accumulation, cross-contamination, and equipment cleaning. The dry nature of grain products makes them prone to dust generation, which can settle in machinery crevices and lead to microbial growth. Regular cleaning and maintenance are critical, but downtime can be costly. Hygienic machinery components and sanitary conveyor parts are indispensable in ensuring food safety and product quality in cereal and grain processing. Investing in high-quality, food-safe components helps processing facilities comply with industry regulations and achieve operational efficiency. From milling to packaging, maintaining the highest hygiene standards is key to delivering safe, high-quality cereal and grain products to consumers. Implementing hygienic design principles and utilizing specialized components such as IP67 bearing units, sanitary seals, and food-grade conveyors can significantly reduce contamination risks and enhance productivity in the cereal and grain processing industry.
Enhancing Hygiene in Cereal and Grain Processing: A Focus on Hygienic Machinery Components and Sanitary Conveyor Parts
The Role of Hygienic Machinery in Cereal and Grain Processing
Milling is the initial and one of the most critical steps in grain processing. The machinery used, such as roller mills and hammer mills, must be constructed from non-corrosive, food-grade materials to prevent contamination. Sealed bearings, sanitary gaskets, and smooth surfaces are essential features of hygienic milling equipment. Proper alignment and hygienic leveling feet also ensure machinery stability, reducing vibrations and cross-contamination risks.
Extruders are used for shaping grain-based snacks and breakfast cereals. They are typically high-pressure systems that require robust, sanitary components capable of withstanding extreme temperatures and pressures. Stainless steel, especially 316L, is the preferred material for parts exposed to product contact, while sanitary couplings and FDA-approved elastomers ensure no harmful substances leach into the food. In addition, hygienic seals and wear-resistant bushings in the extruder help maintain high standards of hygiene.
Roasting equipment is commonly used in the production of breakfast cereals and grain-based snacks to achieve the desired flavor and texture. Hygienic roasters are designed with smooth, easy-to-clean surfaces and minimal crevices to avoid the buildup of residues. The roasters must also be equipped with sanitary temperature controls and heat-resistant gaskets to prevent contamination from high temperatures and thermal cycling.
The final step in cereal and grain processing is packaging, where maintaining hygiene is paramount. Packaging machinery includes filling, sealing, and labeling systems that must handle food products with care and precision. Hygienic packaging components, such as IP67-rated waterproof sensors, sanitary conveyor belts, and food-safe lubricants, ensure that the product remains uncontaminated until it reaches the consumer. Additionally, using anti-microbial conveyor parts can further reduce the risk of bacterial growth during the packaging process.Key Hygienic Components for the Cereal and Grain Industry
Conveyors are ubiquitous in cereal and grain processing, moving product between milling, extruding, roasting, and packaging stages. Hygienic conveyors are designed with smooth, easy-to-clean surfaces, minimal contact points, and food-safe materials. They often feature quick-release belts, allowing operators to perform fast and thorough cleaning without extensive downtime. Modular belts made of FDA-approved plastics and stainless-steel roller chains are commonly used, ensuring that the conveyors meet strict food safety standards.
Bearing units in food processing environments must withstand regular washdowns without compromising performance. IP67 waterproof bearing units, made from stainless steel and equipped with hygienic seals, prevent water and detergent ingress, reducing the risk of contamination. In cereal and grain processing, where dust and particulates can accumulate, sealed bearing units are particularly advantageous in preventing product buildup and minimizing maintenance needs.
Proper alignment and stability of machinery are essential in maintaining production efficiency and product safety. Hygienic machine leveling feet, constructed from non-corrosive materials like 304 or 316L stainless steel, ensure that equipment remains stable, even during intensive operations. These leveling feet are designed with minimal threads and crevices, preventing the accumulation of dust and debris, and are easy to adjust for cleaning.
In cereal and grain processing, sanitary seals and gaskets are essential for maintaining hygiene and preventing contamination between different stages of processing. These components must withstand temperature fluctuations, pressure changes, and exposure to various cleaning agents. High-performance elastomers such as EPDM, silicone, and PTFE are often used to ensure chemical resistance and food safety compliance.Addressing Common Hygiene Challenges in Grain Processing
To mitigate dust issues, processing facilities can employ dust-tight seals and use negative air pressure in critical areas. Hygienic design principles, such as sloped surfaces and rounded corners, help prevent dust accumulation and make cleaning more efficient.
Cross-contamination is a serious concern, especially when processing gluten-free grains or cereals. Using hygienic conveyors with easily replaceable belts and sanitary machine parts reduces the risk of cross-contamination. Separate processing lines for allergen-free products can also ensure compliance and protect consumer health.
The dry nature of grain processing can make cleaning challenging, as water cannot always be used. Instead, facilities rely on dry cleaning techniques like air blowers and vacuum systems. However, critical components like conveyors and extruders must be designed for easy disassembly to facilitate thorough cleaning. Using hygienic machine parts that are resistant to wear and tear ensures that regular maintenance does not compromise production hygiene.Enhancing Hygiene in Cereal and Grain Processing
A Focus on Hygienic Machinery Components and Sanitary Conveyor Parts
Contact
Articles