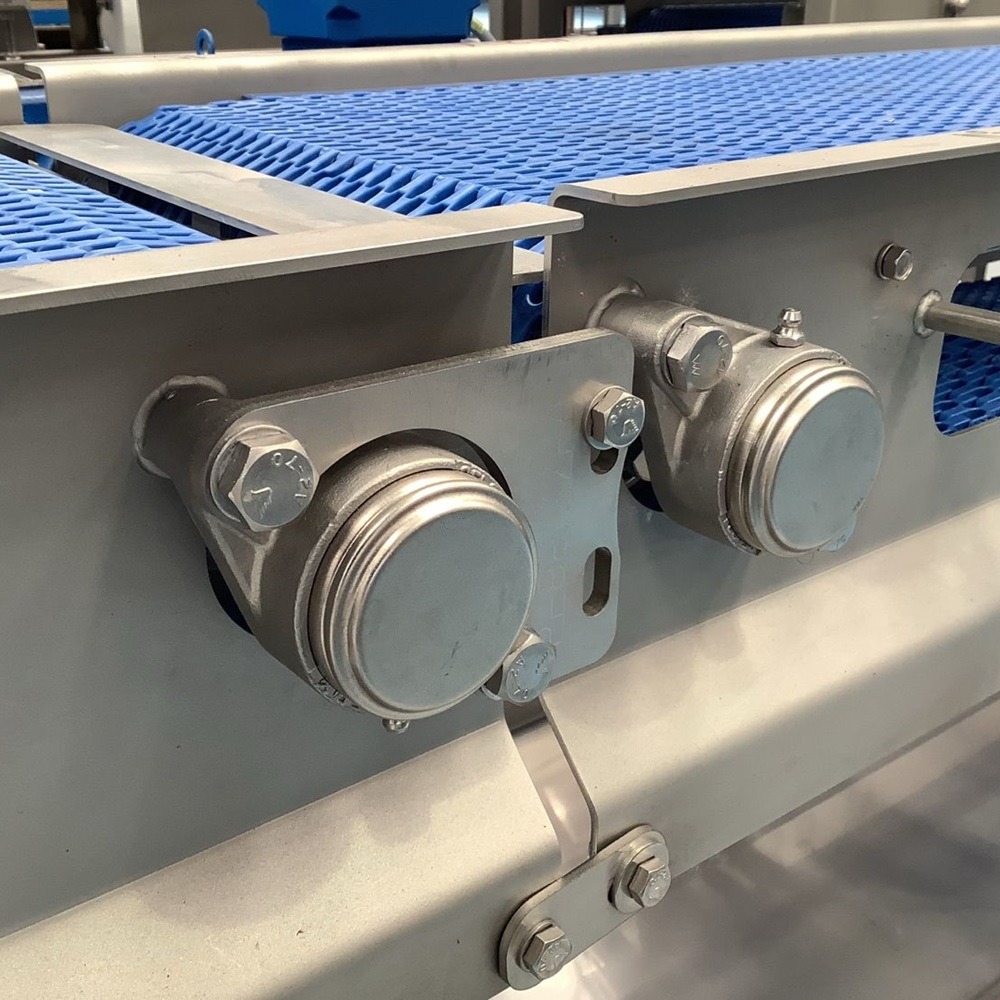
Beverage Processing
The beverage processing industry is one of the most dynamic sectors within food and drink manufacturing. To ensure the highest standards of safety, quality, and efficiency, hygienic machinery components and sanitary conveyor parts are essential. Whether producing and filling juices, soft drinks, coffee, tea, beer, wine, or spirits, beverage manufacturers must meet stringent hygiene regulations and ensure contamination-free production. This article explores the critical role of hygienic components and conveyor parts in the beverage industry, focusing on common equipment used, key applications, and how these parts contribute to safe and efficient operations. Beverage processing requires a controlled environment where every component, from pumps and valves to conveyors, must comply with strict hygiene standards. Given the nature of beverage production, which involves handling liquid ingredients that are highly susceptible to contamination, machinery must be designed to facilitate easy cleaning and prevent bacterial growth. Equipment used in the sector must not only deliver consistent performance but also minimize downtime by offering quick maintenance and cleaning features. The use of high-quality materials such as stainless steel, FDA-approved plastics, and sealed bearing units ensures that the machinery can withstand regular exposure to water, cleaning agents, and fluctuating temperatures. Hygienic machinery components and conveyor systems must also be resistant to corrosion, prevent product build-up, and ensure that no foreign particles compromise the beverage’s integrity. Juice production is a delicate process that requires careful handling of raw fruits and vegetables. Equipment such as hygienic pumps, filtration units, and pasteurizers are essential to remove unwanted particles and bacteria, ensuring a smooth, pure product. During the filling process, sanitary conveyor systems transport bottles or cartons through a filling line equipped with precision bottle fillers. To maintain hygiene, conveyor components are designed to prevent the accumulation of juice residues that could lead to microbial growth. Producing carbonated beverages like sodas involves multiple stages, including mixing, carbonation, and filling. Carbonation systems must be hygienically designed to prevent CO2 leakage and maintain product consistency. Bottle fillers and canning lines equipped with hygienic components ensure that the product is filled without losing carbonation levels. Sanitary conveyor belts play a pivotal role in transporting cans and bottles smoothly between stages while ensuring that the equipment remains free from contamination. Hygiene is a top priority in coffee and tea processing, where even minor contamination can lead to off-flavors or reduced product quality. Hygienic equipment, such as stainless steel mixers, grinders, and pasteurizers, must be easy to clean and maintain. Conveyor systems used in coffee and tea facilities often incorporate food-grade belts and corrosion-resistant components to handle dry and wet processing stages. For packaging, bottle fillers and sealed bearings are used to prevent product contamination during the filling process. In breweries, wineries, and distilleries, hygiene is essential for maintaining product quality and preventing unwanted fermentation. Hygienic components such as sanitary pumps, stainless steel fermentation tanks, and clean-in-place (CIP) systems are integral to these processes. Conveyor systems must be designed to handle heavy bottles and kegs, ensuring smooth transportation with minimal vibrations. Hygienic bearing units and sealed joints prevent the infiltration of moisture and bacteria, ensuring the safety and longevity of the equipment. The beverage processing industry relies on a variety of specialized equipment to achieve high efficiency and meet safety standards. Below are some of the common machines and components used: Hygienic machinery components and sanitary conveyor parts are vital for maintaining the safety and quality of beverages. Key benefits include: In the beverage processing industry, maintaining stringent hygiene standards is not just a matter of compliance but a critical factor in ensuring product quality and consumer safety. Hygienic machinery components and sanitary conveyor parts play a pivotal role in achieving these objectives. From production to filling, every component must be meticulously designed and maintained to prevent contamination and optimize performance. By investing in high-quality hygienic components, beverage manufacturers can safeguard their products, streamline operations, and remain competitive in an increasingly regulated market.
Hygienic Machinery Components and Sanitary Conveyor Parts for Beverage Processing
Understanding the Importance of Hygiene in Beverage Processing
Key Applications in Beverage Processing
1. Production and Filling of Juices
2. Carbonated Soft Drinks and Soda
3. Coffee and Tea Processing
4. Beer, Wine, and Spirits Production
Common Equipment in Beverage Processing
Benefits of Hygienic Machinery Components and Sanitary Conveyor Parts
Hygienic Machinery Components and Sanitary Conveyor Parts for Beverage Processing
Contact
Articles